What is CUI?
Corrosion under insulation, or CUI, refers to a type of corrosion that damages carbon, low-alloy, and austenitic stainless-steel equipment (e.g., pipework and pressure vessels) that are fitted with thermal insulation and protective cladding layers.
CUI is classified as ‘external’ corrosion because it forms on the outside of pipework and vessels beneath the protective insulation and cladding. It is caused by the inevitable penetration of water within cladding systems over time, which then subsequently proceeds to permeate through/between insulation layers. When moisture contacts the underlying pipework/vessel, dangerous corrosion develops. In the case of carbon steel, corrosion growth rates under insulation are reported to be up to 20x faster than those in standard atmospheric conditions.
A recently published review conducted by the Massachusetts Institute of Technology credited ExxonMobil with the statistic that approximately ~50% of pipework maintenance costs can be attributed to CUI. Additionally, a recent article published in Oilfield Technology stated that CUI is a significant contributor to fugitive emissions, which poses a major operational, safety and economic challenge for operators in the upstream oil and gas industry. Over 20% of the major oil and gas accidents reported within the EU since 1984 were associated with CUI. The article also highlighted that many assets on the UK Continental Shelf are operating beyond their original design life and that ~60% of pipe failures can be attributed to CUI. The International Energy Agency estimates that, for net zero to be achieved, fugitive methane emissions need to reduce by 75% by 2030. Early detection and repair of failing pipework will reduce associated fugitive emissions of methane by 14%.
Whilst CUI is a significant problem from a structural materials perspective, it also poses operational, environmental, and economic risks within petrochemical processing facilities. As an example, in 2006, a leak caused by CUI occurred in a petrochemical plant. The resulting fire caused ~$50mn in facilities damages and substantial damage to the environment.
Initially, thermal insulation was used only in high-temperature (+150C) applications for energy conservation reasons. Therefore, because moisture evaporates at elevated temperatures, CUI was not an issue. After the petroleum shortages during the 1970s, thermal insulation was applied more generally throughout petrochemical plants to reduce processing costs. Moisture/water does not evaporate as quickly at lower temperatures, and therefore CUI became an issue.
As we move towards a net-zero society, we must embed an energy-efficient mindset throughout the wider industry and our daily lives. Therefore, to reduce energy loss during the upstream topside production and midstream processing phases, we need to ensure pipework and vessels are coated, insulated and cladded using the most energy-efficient systems.
Over the years, major advances have been made in the development of advanced coatings, high-performance insulations, and robust non-metallic cladding systems. When used in combination, these modern solutions reduce the probability of CUI occurring, thereby reducing processing plant lifecycle costs, and improving energy efficiency.
Whilst the probability of CUI occurring is reduced through the implementation of the aforementioned technologies, the threat remains severe when CUI does form in any given location within a processing plant. The industry remains committed to plant-wide inspection campaigns to further minimise the chances of a leak, caused by CUI, resulting in environmental damage.
Since 2019, in collaboration with the UKs Net Zero Technology Centre, Subtera has developed and field-tested a novel screening camera to simultaneously detect CUI and moisture beneath modern cladding and insulation systems. Over the past 18 months the handheld camera, named Pi, has been successfully evaluated at facilities throughout the UK and Europe.
Historically, the industry has detected CUI through the laborious, costly, and time-consuming method of physically removing cladding and insulation systems to perform visual inspections. All of these activities introduce additional challenges and risks, especially where CUI has to be confronted through an intervention and remedial campaign involving scaffolding and other construction activities. Subtera’s technology detects hidden CUI and moisture in real time without removing non-metallic cladding.
Subtera is focused on developing screening solutions that simplify CUI and moisture detection, help to reduce leaks, and subsequently help us to achieve net-zero together.
Share article:
You may also like to read
Signup to our newsletter
To hear the latest from Subtera about our technology, industry insights, case studies and company news, enter your email and we’ll send updates directly to your inbox.
By signing up, you agree to our privacy policy.
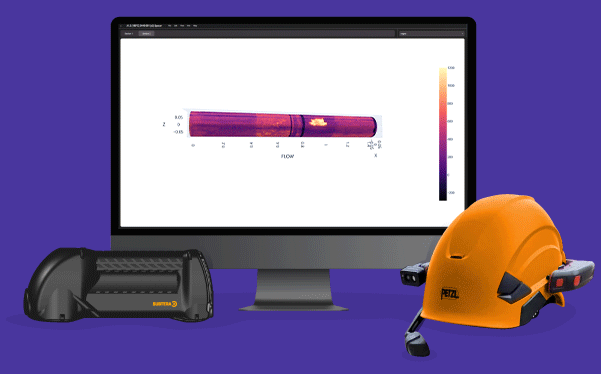